How a new helmet evolves from the drawing board to final production
TEXT // JACK THOMPSON | PHOTOS // BBB CYCLINGThere are aero helmets and there are lightweight helmets. Each claiming to ‘do this’ and ‘do that.’ … Obviously, the primary purpose for wearing a helmet, is to protect the head in case of an accident. Helmet manufacturers would have you believe that ‘their latest’ helmet is the greatest, be it because of the aero advantage it delivers to the rider, or the weight saving it offers (weight weenies rejoice!).
When looking at ‘top of the range’ helmets from the well-known brands, cost is often a prohibitive factor for consumers with prices upwards of $250 being the norm. ... But here’s where things get interesting. What if I told you that Dutch cycling industry leaders, BBB, had designed and manufactured a helmet that possessed all the latest tech currently on offer and bundled it up into a package for 50 percent of the cost? Most would probably laugh and say, ‘you’re dreaming.’
The reality is, that I’m not… When I visited the BBB Cycling headquarters in the Netherlands last year, I was let in on a little secret. Over the past couple of years, while their competitors have been releasing new helmet year after year, BBB have quietly been working away on one of their most exciting projects yet. Low and behold, ‘The Maestro’ helmet.
Designing an industry leading helmet
Building on the success of their Icarus and Falcon helmets, worn by professionals from teams such as Vaconsoleil, Équipe cycliste Groupama–FDJ and WantyGobert Cycling Team in the ranks of the pro-peloton over the last five years, BBB saw a unique opportunity to carefully design an industry leading helmet that combines impressive levels of ventilation (for hot days and climbing) along with world class aerodynamics (for flat days at high speed) at a fraction of the price of their competitors.
With input from Arnaud Demare, Ramon Sinkeldam and the rest of the Équipe cycliste Groupama–FDJ Team (to name a few), BBB has now released an impressive feat of engineering, to the consumer market, at price points never seen in this category of head protection.
From the drawing board to final production
So, what exactly goes into the development of a new helmet such as the Maestro at BBB’s R&D headquarters in Leiden and how does this concept evolve from the drawing board to final production? First things first. The talented R&D team looks at the demand for a new product. In the case of the ‘Maestro’ helmet, the main driver was to produce a highly ventilated helmet that also offered high levels of aerodynamics in a complete package that would retail for less than 100 euros. From here, the team looks at how they can add value to ensure the products they are developing stand out from the competition.
Moving forward and with the concept drawings complete (this can take months and months of hard work), various 3D models are printed in house so that the actual size and shape can be assessed and reviewed. As is the case with many helmets, when perched on the head of the rider, they look ‘mushroom-esque.’ This is a feature that BBB are adamant that their helmets DO NOT possess and in the case of the Maestro, the sleep lines and low profile are quite the opposite.
Following on from the 3D models comes the first actual prototypes (often in outlandish patterns and colours.) Again, during this phase, there is a huge amount of consultation both internally and with the professional riders to ensure that the shape and fit are perfect. Refinements take place slowly over months of field testing in various conditions.
Putting it to the test
The next step involves the arduous testing phase where the helmet is put to the test from a safety perspective. Although passing the European standards is often not a problem, the difficulty comes in passing the overseas standards, like the American CPSC and its Australian counterparts as the methods of testing are quite different. This explains why a lot of helmets are not available for the Australian market.
With the testing complete, the final product goes into the production phase and is then sent to the various markets.
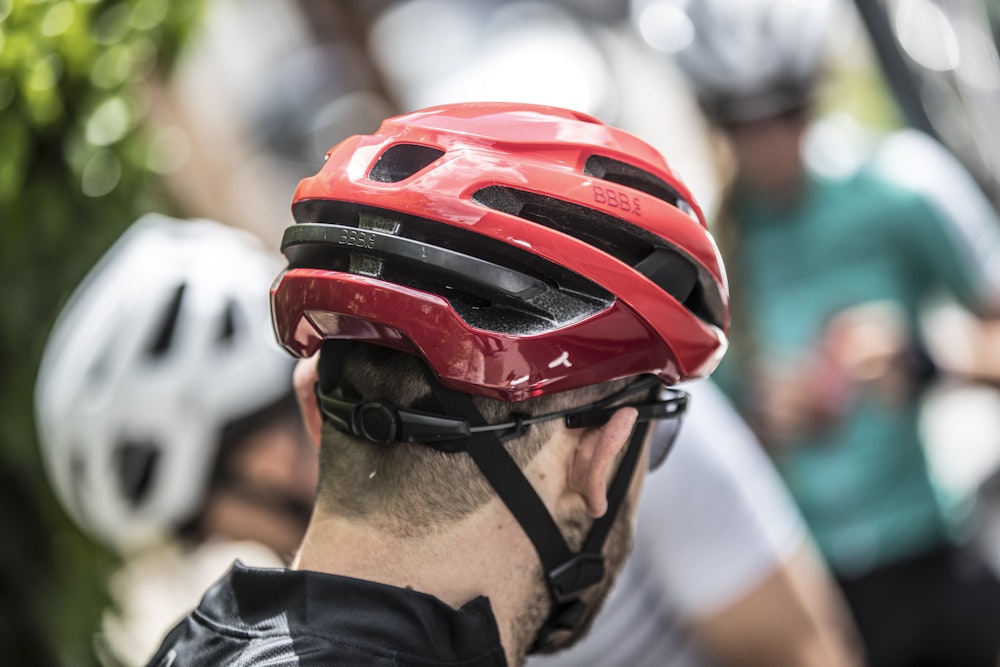
The final product
The above process ‘reads easy’ however in practise, the process can take years, especially in the case of the Maestro where there are three big drivers. In the case of an aero helmet for example, there is generally just the ‘aerodynamic driver,’ but as outlined above, the brief for the Maestro was ventilation, aerodynamics and cost combined. These are drivers that are often looked at by brands as three individual helmets, this explains the longer development phase that the Maestro has been through.
At the time of my visit I was unable to physically test the Maestro on the road. But, I was able to try the helmet on at the BBB HQ and can ‘hand on my heart,’ say that it is a seriously nice piece of kit. Nowadays I enjoy riding with this piece of art on my head, conquering all my challenges. The helmet will be available in a raft of different colours.